Why recycle waste tires?
The total amount of waste tires in my country each year has long been among the top in the world. According to data released by the Ministry of Industry and Information Technology, my country produced approximately 330 million discarded tires in 2019, of which approximately 290 million were scrapped car tires, accounting for 88%. The number of discarded tires in our country will continue to grow, with an annual growth rate of 8% to 10%.
Waste tires are known as “black pollution”. The large accumulation of discarded tires not only takes up land, but also seriously damages the environment. Since the time required for tire decomposition is uncertain, waste tires cannot biodegrade. The heavy metal elements such as lead, chromium, and cadmium contained in them may pose a threat to human health and the environment if not handled and managed properly. Waste tires stacked in the open for a long time not only occupy a large amount of land resources, but also easily breed mosquito-borne diseases, seriously damage the natural environment, and present fire hazards. Therefore, how to deal with the increasing amount of waste tires has become an urgent environmental issue and a support issue for industrial development.
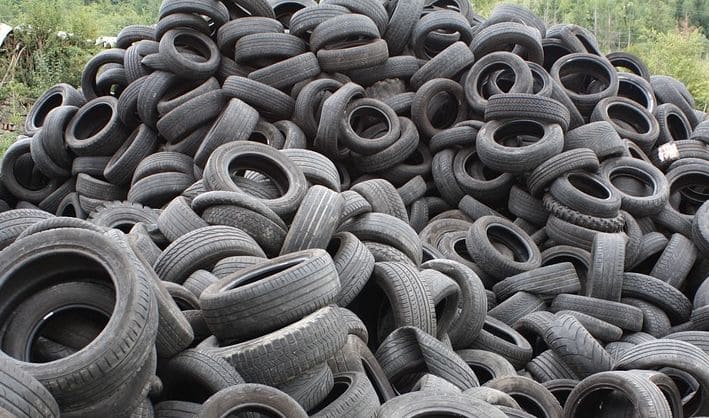
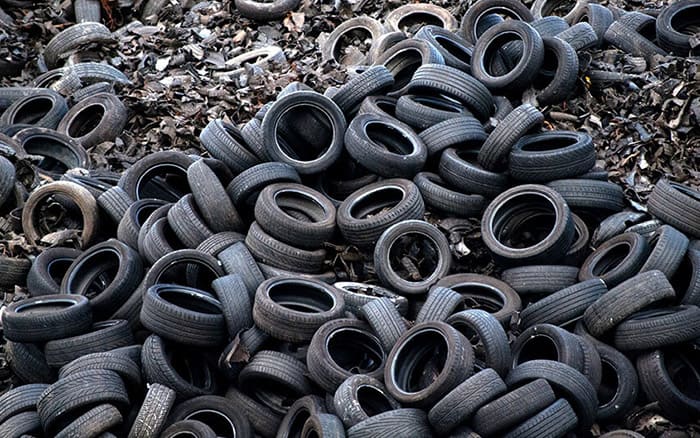
In addition to conventional treatment methods, waste tires can be recycled through tire shredders, tire recycling systems, tire shredding machine and other equipment to further promote the resource utilization of waste tires.
Application of tire shredder
Tire shredder is one of the important tools for waste tire processing. By using a tire shredder, waste tires can be shredded into small pieces efficiently, making subsequent processing easier. This equipment ensures efficient shredding and fine shredding of tires, creating more favorable conditions for other processing stages.
Innovations in tire recycling systems
The introduction of advanced tire recycling systems can convert waste tires into usable resources more efficiently. These systems use innovative technology to separate different parts of the tire, such as rubber, metal and fiber, for more precise recycling and reuse. Tire recycling systems play a key role in resource recovery, providing a sustainable source of resources while reducing waste.
Automation of tire shredding machine
The automation technology of tire shredding machine continues to develop, making the processing of scrap tires more intelligent and efficient. By introducing advanced automated control systems, tire shredding machine can more accurately control the shredding process, improve production efficiency, reduce manual intervention, and reduce labor costs.
Waste tires can be processed through various methods such as prototype utilization, old tire retreading, recycling, auxiliary fuel and thermal cracking and power generation technology processing:
Recycling:
Waste tires can be crushed into rubber powder, which is widely used in highways, airport runways, flame retardant materials, rubber and plastic soles, waterproof materials, sports runways and other fields. Rubber powder can also be produced after desulfurization and used to make rubber products such as hoses and tapes.
Auxiliary fue:
The calorific value of waste tires is over 8,000 kcal, which is 5,000 kcal higher than that of coal. The ash remaining after combustion is also equivalent to that of coal, so it is very suitable for industries that require high thermal energy. In the United States, Japan and many European countries, many cement plants, power plants, paper mills, steel plants and smelting plants use waste tires as fuel, with good results and reducing corporate production costs to a certain extent.
Thermal cracking:
The principle of thermal cracking is to place waste tires in an oxygen-deficient or inert gas for incomplete thermal degradation, which can produce liquid and gaseous hydrocarbons and carbon residues. This technology first crushes the waste tires into pieces and then sends them to the thermal cracking reactor. After being heated in the reactor, a thermal decomposition reaction occurs. Next, the gaseous products are separated into oil and vapor through the condenser, and the fuel oil is condensed and used as fuel. In addition, the separated non-condensable flammable gas is sent to the combustible gas generator for power generation through desulfurization, which solves the problem of secondary air pollution. Except for a small amount of electricity for the thermal cracking system equipment, most of the total power generation can be connected to the grid for power supply. , the solid product in the reactor is mainly carbon black. The crude carbon black is separated from the steel wire through magnetic separation. The crude carbon black is further processed to obtain carbon black for commercial application.
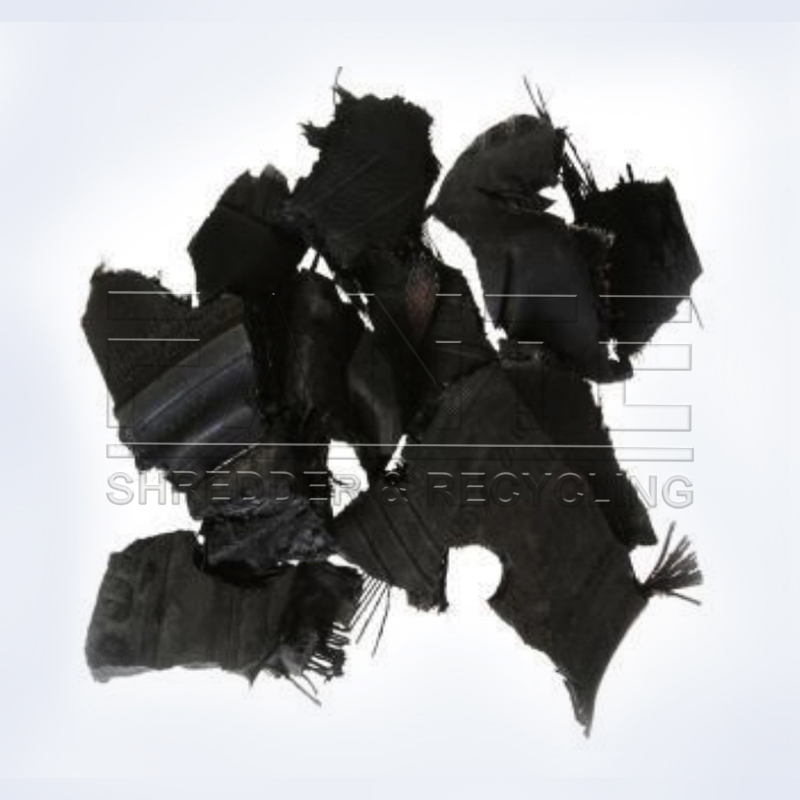
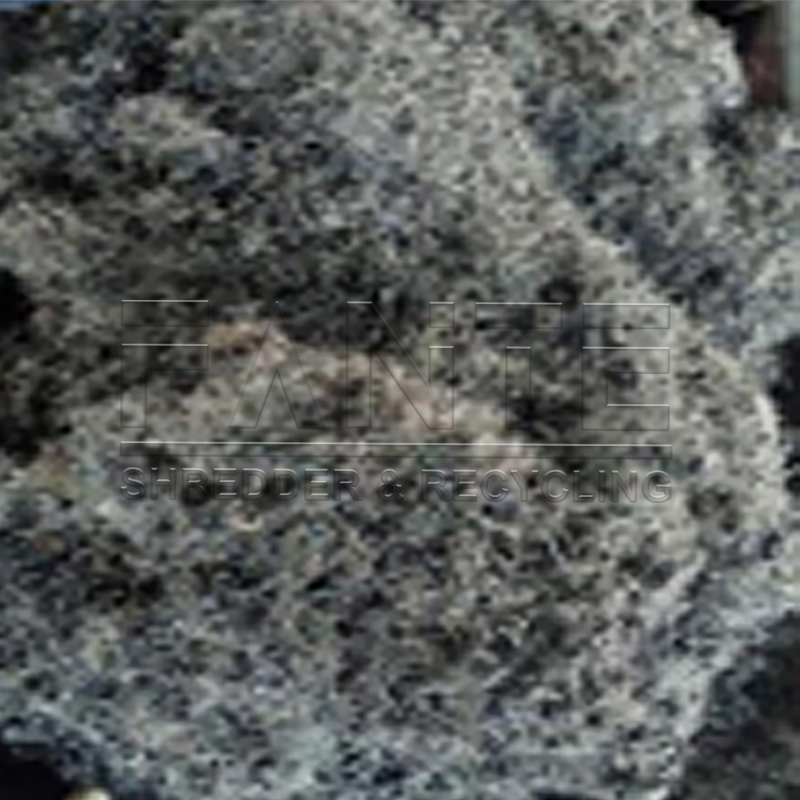
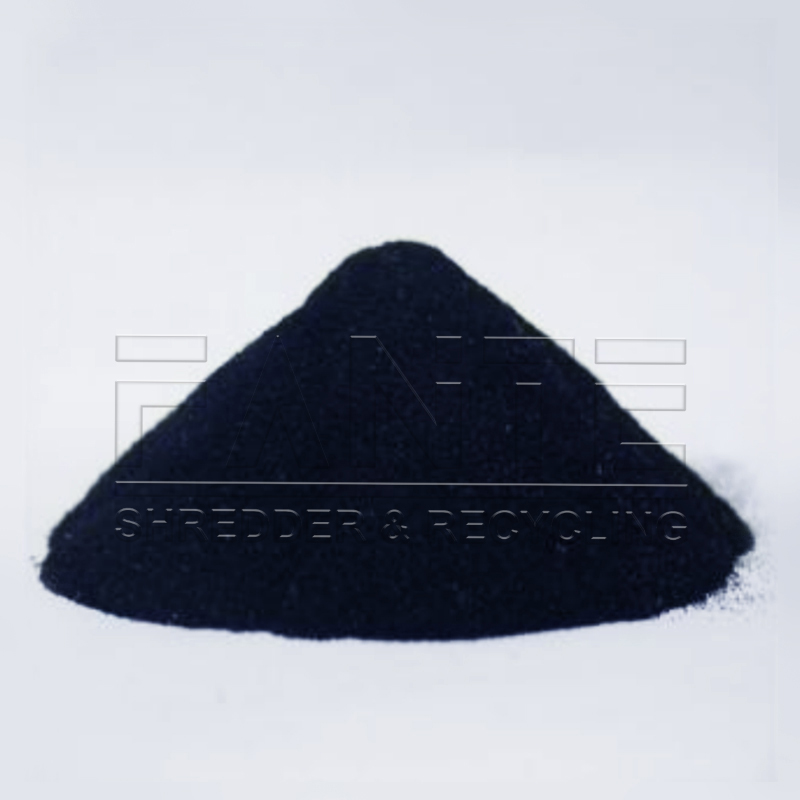
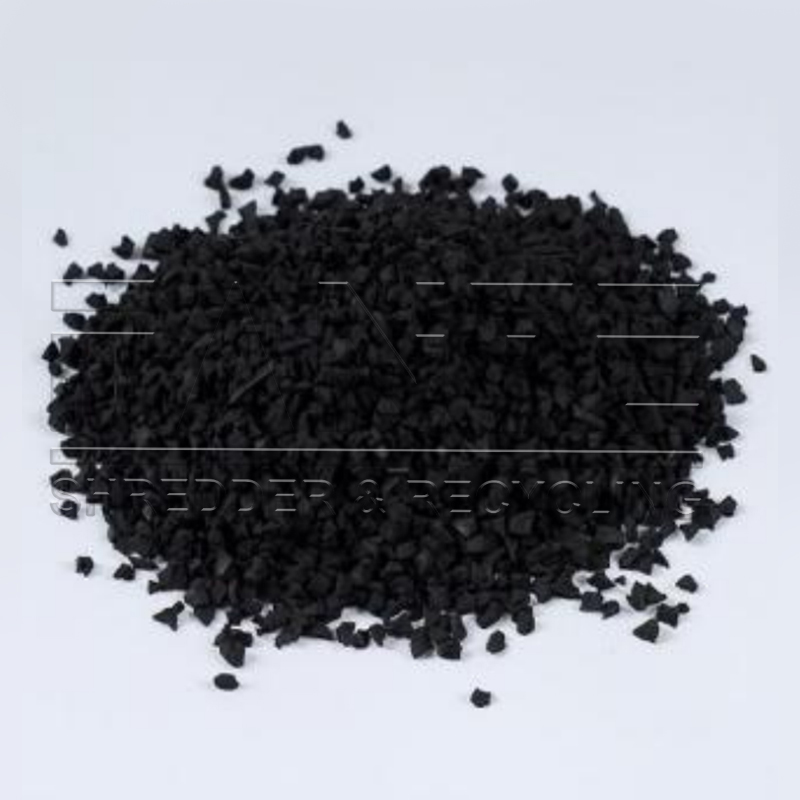